The fuel shutoff solenoid, a small yet crucial component in numerous types of engines, plays a pivotal role in regulating fuel flow, engine efficiency, and safety.
This seemingly simple device, comprised of an electromagnetic coil, a plunger, and a spring, harnesses the principles of electromagnetism to toggle the fuel supply.
Despite its diminutive size, it can profoundly affect the performance and reliability of an engine.
Understanding its structure and functions may offer new insights into how technological advancements in something as elementary as an on-off switch can significantly contribute to engine performance and safety.
Table of Contents
The Structure of A Fuel Shutoff Solenoid
The arena of automobiles and gasoline-driven devices presents a vibrant interplay of numerous intricate components maneuvering in sync, to ensure an optimum user experience.
One such critical component is a fuel shutoff solenoid. A centralized concept in many gasoline-driven engines, this elusive device appears daunting to the layman.
However, to a passionate academic like us, unveiling such a complex mechanism presents an opportunity to dwell deeper into the fascinating world of applied science.
A fuel shutoff solenoid is essentially an electromagnetic device employed within internal combustion engines to control the flow of fuel from the fuel pump towards the engine.
The precise functionality of these solenoids have birthed a profound impact on fuel efficiency, engine performance, and thermal management.
Embarking on the journey to deconstruct a fuel shutoff solenoid, one finds oneself confronting four fundamental components – the plunger, the coil, the stop, and the return spring.
- The Plunger: At the heart of this device lies the plunger. Often a cylindrical metal pin, its movements enable or inhibit the fuel flow. A fascinating dance of precision and synchronization!
- The Coil: Encircling the plunger is the coil. It creates the electromagnetic field vital in actuating the plunger. It exemplifies the fine utilization of electromagnetics in mechanical systems.
- The Stop: Acting as a restraint, the stop governs the extent of movement allowed towards the plunger. A feat achieved through immaculate calibration!
- The Return Spring: Contrasting the role of the coil, the return spring reins back the plunger when the coil is de-energized, resulting in the halting of the fuel flow.
The plunger, coil, stop, and return spring come together to constitute the verse of a fuel shutoff solenoid.
However, the elegance of this narrative lies in their impeccable configuration, which maintains the delicate balance necessary for fuel regulation.
Primarily, the plunger is situated within the coil, with the stop limiting its extension. Once energized, the coil creates an electromagnetic field, thereby drawing the plunger towards the stop.
This movement enables the flow of fuel from the pump to the engine. However, once the coil is de-energized, the return spring asserts its force, propelling the plunger away from the stop and ceasing the fuel flow.
The configuration of these four fundamental components and their collective function epitomize the essence of a fuel shutoff solenoid, highlighting how sophisticated principles of physics can elegantly merge with practical mechanical requirements.
Though it may be a single cog within the vast machinery of an engine, the fuel shutoff solenoid exhibits the harmonious ballet of multiple disciplines – embodying both chapters from electromagnetism and lessons in mechanical design.
Indeed, it is this interdisciplinary dance that makes automotive science a realm brimming with limitless wonder.
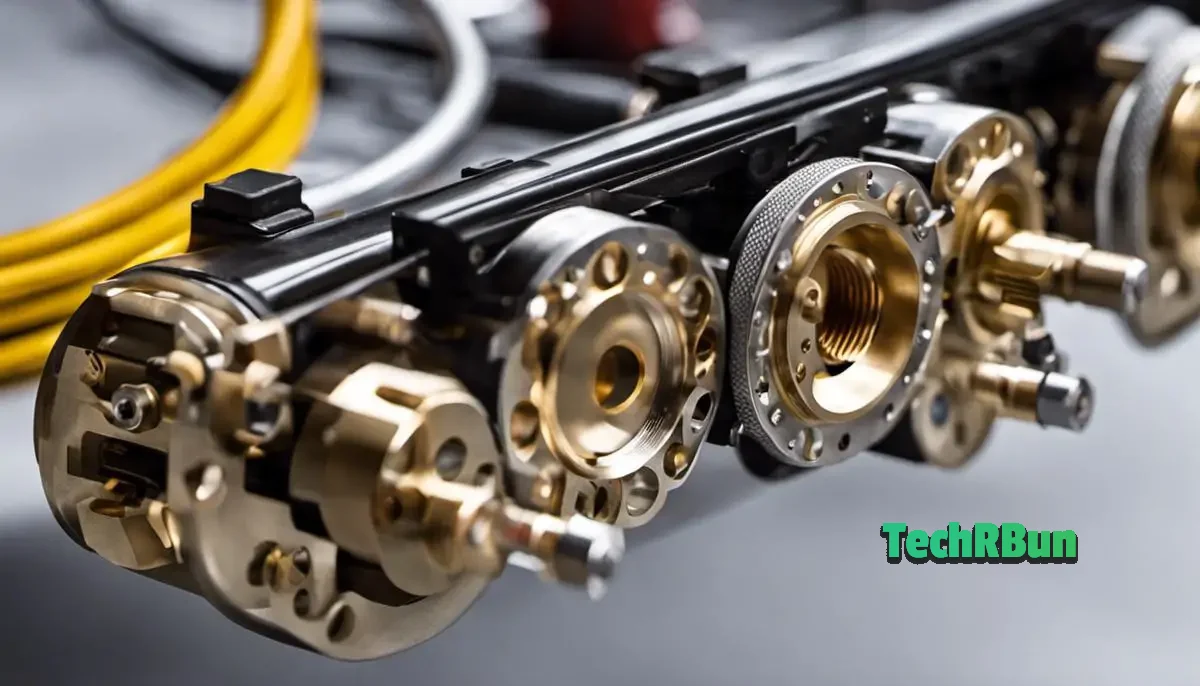
Operation of A Fuel Shutoff Solenoid
Continuing our discourse on the quintessential role of a fuel shutoff solenoid in a machine, let’s elucidate its operation.
After discussing the core components and dynamics, it is crucial to comprehend the activation process and significance of electric control in the functionality of this crucial piece of gear.
Marrying the knowledge of physics, engineering and automotive principles, the operation of a fuel solenoid primarily revolves around changes in electric currents.
Upon receiving a voltage signal from the engine control unit (ECU), the coil wrapped around the plunger within the solenoid acts as an electromagnet.
This magnetic field induces the plunger to move within its cylindrical chamber, defying the tension of its return spring, subsequently opening or closing the fuel valve.
During the initiation phase—the moment the ignition switch is powered on—the amount of current flowing into the coil is high.
Consequently, the strong magnetic force pulls the plunger against the stop, opening the valve and allowing fuel to reach the engine.
This process is crucial at the start-up phase as it bypasses the need for an operator to manually initiate the process.
As the engine reaches its operating temperature, the need for a high quantity of fuel diminishes. At this point, the ECU reduces the electric current flowing into the coil.
Consequently, the magnetic field weakens and the return spring pulls the plunger back to its original position, adjusting the valve to limit the fuel supply—thus ensuring efficient fuel consumption and minimal engine wear.
In essence, the bilateral movement of the solenoid’s plunger—under the interplay of magnetic force and spring tension—dictates the fuel flow and therefore, the running condition of the engine.
This governing method understands the delicate balance between ensuring optimal engine performance and facilitating resource efficiency, all while permitting automatic control.
A system failure occurs if the solenoid gets stuck or fails to activate—known technically as solenoid dropout—leading to undesirable engine outcomes such as uncontrolled fuel flow or engine stall.
Preventive maintenance, including regular inspections and solenoid replacements, can greatly mitigate the risk of such issues.
Entering the realm of vehicle electronics and integrating it with the mechanical design, the fuel shutoff solenoid exemplifies the interconnection between different scientific fields in modern technological applications.
Its functioning epitomizes not just the sophistication of mechanical systems, but also the marvels of electrical, automotive, and control engineering—an interdisciplinary symphony in motion.
A testament to the endless possibilities sparked by curiosity, knowledge, and a dash of creativity.
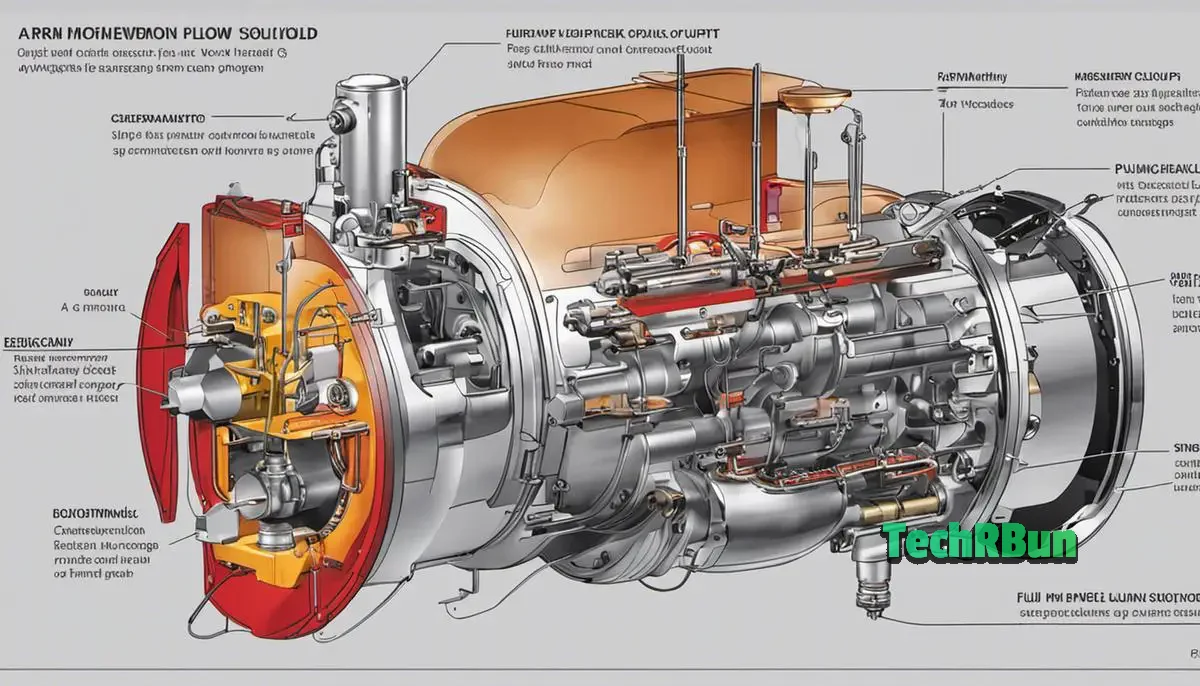
Applications and implications of a fuel shutoff solenoid
Fuel shutoff solenoids are typically used in machinery and vehicles operating with diesel engines, and they play a vital role in their functionalities.
Their use is perennially observed in agricultural machinery, marine applications, generators, light industrial equipment, and in some cases, high-performance race cars.
This broad spectrum of applications underlines the fact that proper operation of a solenoid directly affects the overall performance and durability of the machinery or vehicle.
The process of activation and operation of a fuel shutoff solenoid is inherently influenced by electrical control. It relies on electric currents to function effectively and perform the job it’s designed for.
A vehicular ignition switch influences the flow of electricity toward this solenoid, thus enabling its activation. Upon activation, the solenoid plunger extends to either open or close the fuel passage as per the demand.
Regulating the fuel flow stands as one of the cardinal functionalities of a fuel shutoff solenoid. Its work doesn’t culminate at simply activating or deactivating fuel supply, rather it also adjusts the amount of fuel channeled into the engine.
When the engine requires more power, such as during an uphill drive, the solenoid allows a higher volume of fuel to flow. This aspect underscores its role in fuel economy and overall resource management.
Nevertheless, the same system may entail certain drawbacks that could potentially devolve into system failures.
These complications can ensue from a faulty solenoid, unregulated fuel flow, or failure of the ignition switch to activate the solenoid.
It is critical to monitor these parameters and instigate preventive maintenance measures, such as regular service and timely replacements, to circumvent any catastrophic failures.
Nevertheless, the point to remember is that no system is perfect or failure-proof; there’s always a certain trade-off that needs to be managed to ensure efficient machinery operation.
The well-conceived integration of vehicle electronics and mechanical design in fuel shutoff solenoids illustrates the interdisciplinary nature of this operation.
Automotive science is not confined to a single scientific domain, but it is rather the confluence of multiple disciplines, making it spectacularly intriguing to the discerning mind.
This continual cross-pollination of ideas leads to novel discoveries and improvements in technologies such as the fuel shutoff solenoid, significantly enhancing the performance, safety, and efficiency of modern mechanical and automotive systems.
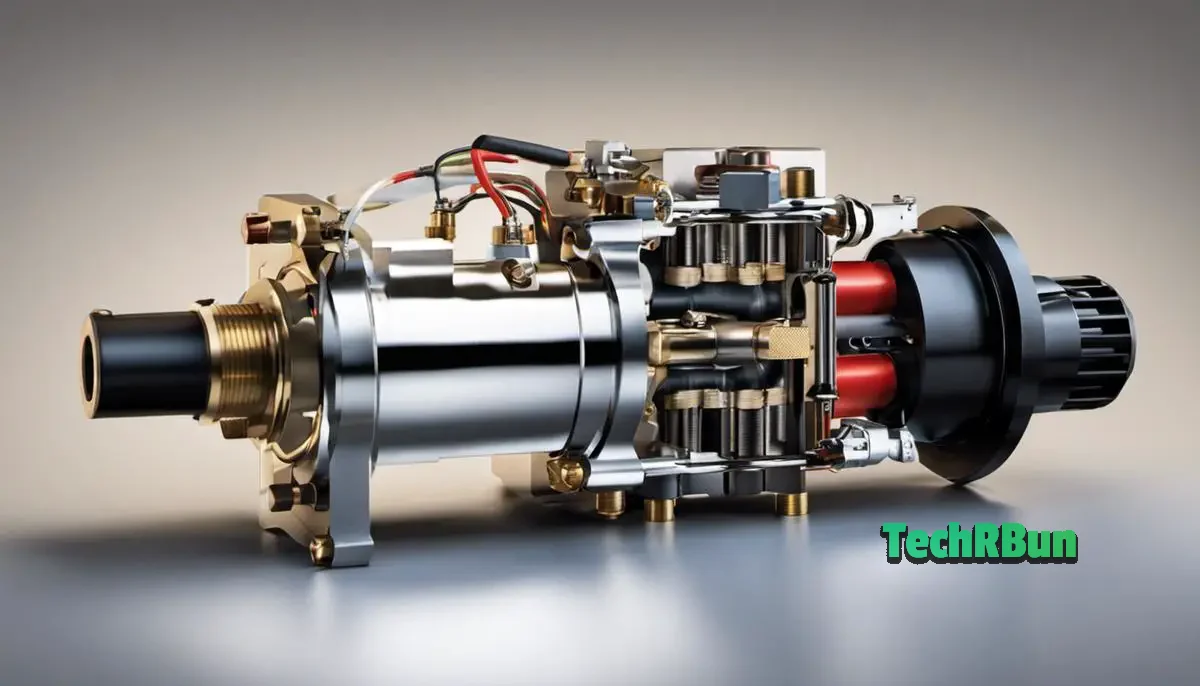
Overall, the fuel shutoff solenoid’s role transcends beyond its application in motors.
It is a testament to how a straightforward, well-engineered solution can tackle multiple challenges, enhancing not only the efficiency and safety of a vehicle, marine engine, generator, or piece of agricultural machinery, but also their environmental impact.
Indeed, when the solenoid fails to operate correctly, the engine’s performance can noticeably drop, emphasizing the solenoid’s fundamental role. By comprehending the repercussions of a functional or dysfunctional fuel shutoff solenoid, we gain an even greater appreciation for its importance in our everyday lives.